
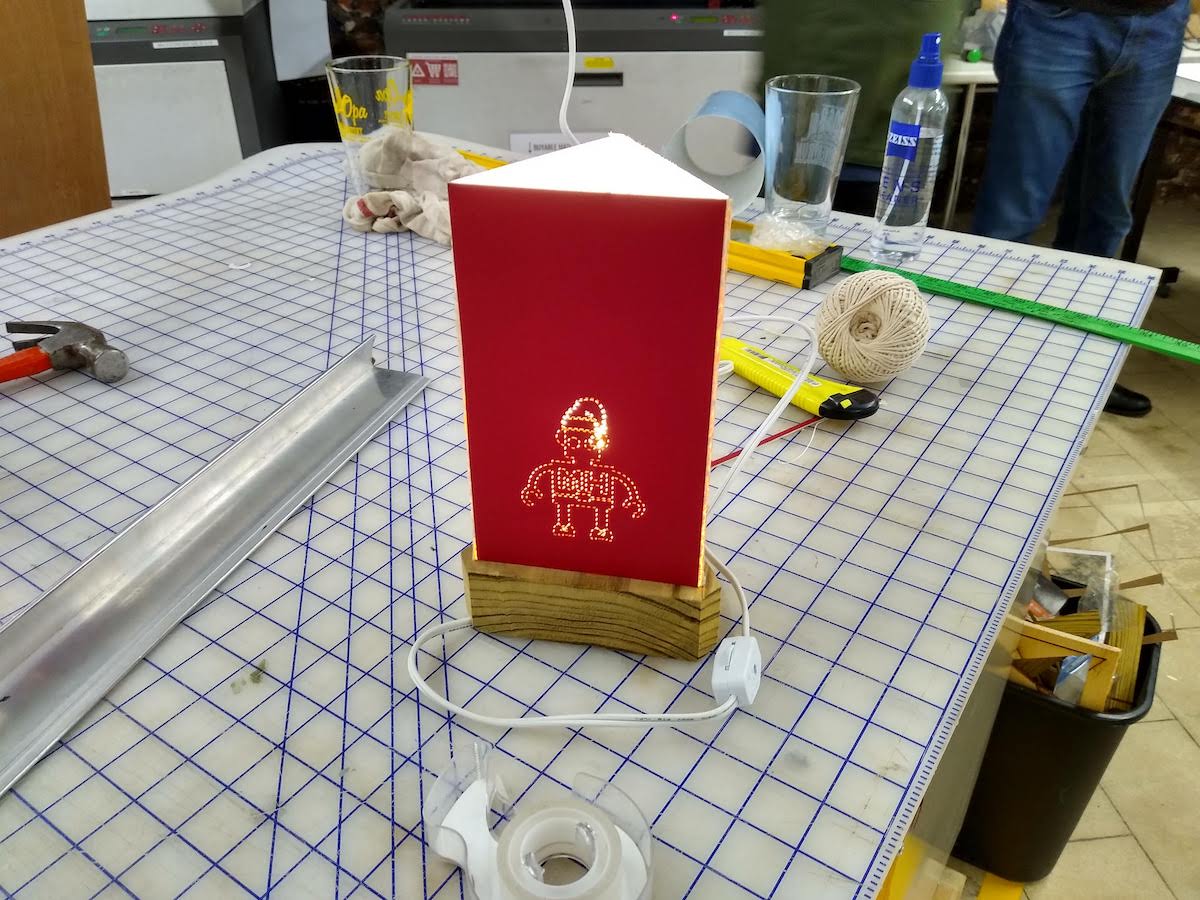

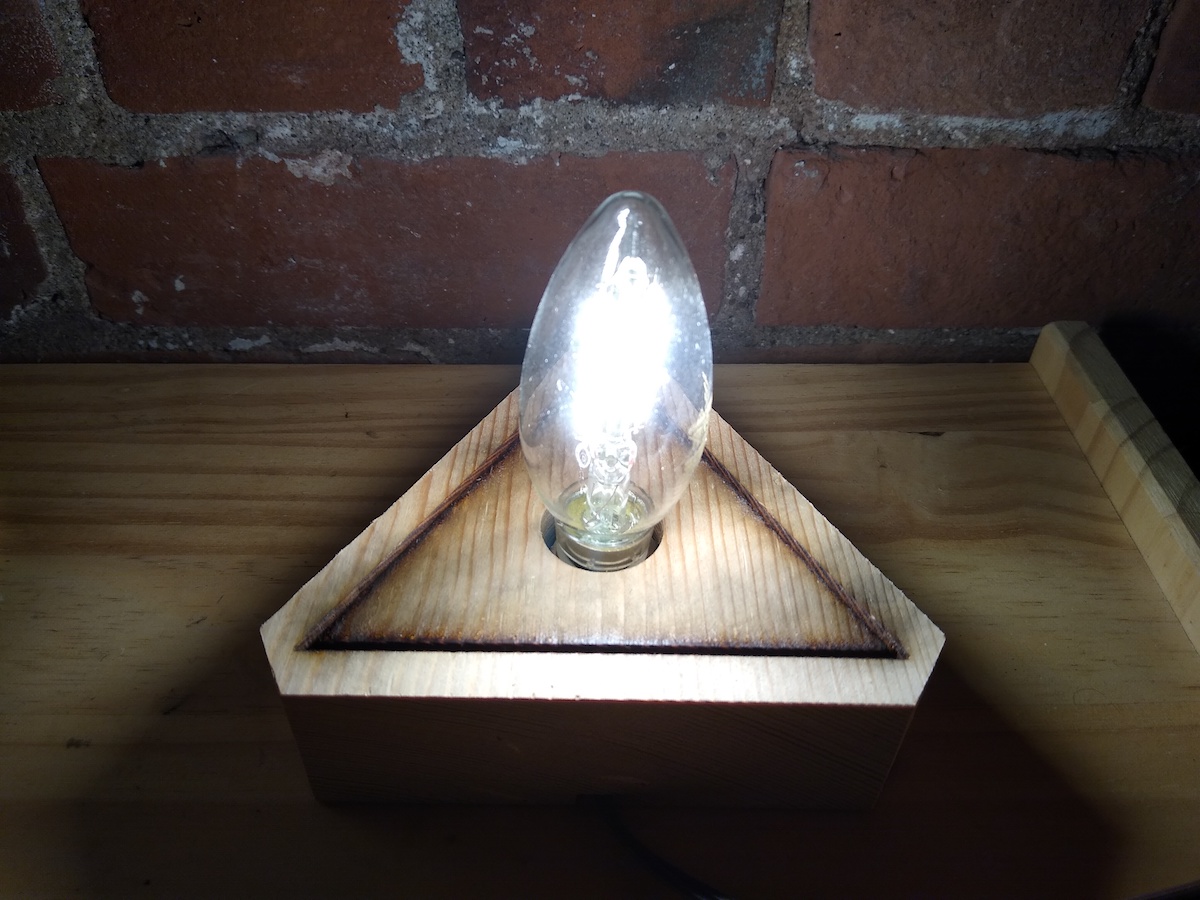
It's a good idea to make the lamp out of a piece of wood at least 18" long: this makes it easier to finish on the miter saw without worrying about chopping your fingers off. That said, at the end of the day using the miter saw means holding it steady freehand, so for the angled cuts, it is probably a better idea to make a jig using a 30-degree wedge and run it through the table saw on a sled. Either way, don't be sloppy (like me): definitely run the last cut on a table saw! This will help avoid the sadness that comes from slipping up on that final corner and ending up with an edge that is obviously angled wrong (see the photo from Step 5 above).
Also, I recommend making two lamp bases at once. (It barely takes any additional time, so why not!) I've set up the laser file (in Project Resources) for the lamp base engraving with two pieces on a 12" piece of wood, but you can move or remove the second set as needed.
This is a cute desk/bedside lamp with an optional laser engraved shade made using a stippling type pattern. It's extremely inexpensive and fairly quick to fabricate. It makes a great gift, especially due to its interchangeable press-fit shade: you can give the base along with one shade as a gift, and then add to it by gifting new shades for other occasions. Depending on the wood/finish and the bulb brightness you choose, it can also look pretty nice without a shade.